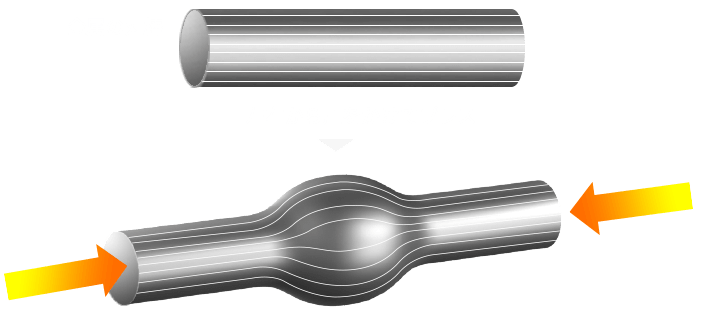
強度に優れたα-βチタンの丸棒を採用。中間部のみを加熱し、1600tの高圧で加圧圧縮し、丸棒の中間部を大きく膨らませた球体にする独自の製法。鍛流線が中央に集まり、金属組織がより密になる。
チタンの丸棒から鍛造する特許技術「加熱圧縮処理鍛造」。一般的なプレス製法では実現できないチタンの「鍛流線」を発生させ、フェース中央部の圧縮率をあげることで、組織をより緻密に鍛え上げ、他に例を見ない打感と反発を生みます。
フェースのCT値が均一になるように設計した適切な偏肉構造です。周辺部の薄肉化とセンター付近の肉厚部にとって、フェースの広範囲でルール限界の反発性能を発揮します。
部分的に鍛造をさらに押し込む「ディンプル鍛造工程」によって、フェースセンター付近の強度を向上し、反発性能を安定させます。
スイートエリアから外れやすい方向に、溝(グルーブ)を設けることで、フェースたわみに指向性を持たせ、ミスヒットの許容性を向上するテクノロジーです。
チタン板材を圧延したフェースを用いる一般的なドライバーに対して、『C01D』は特許技術である 丸棒鍛造製法を採用。金属組織が非常に緻密になり、引っ張り強度や硬度、粘り強さが向上します。
強度に優れたα-βチタンの丸棒を採用。中間部のみを加熱し、1600tの高圧で加圧圧縮し、丸棒の中間部を大きく膨らませた球体にする独自の製法。鍛流線が中央に集まり、金属組織がより密になる。
一般的なフェースの製造は圧延材と呼ばれるチタンの板材をプレス成型するため、鍛流線は生まれない。高度や強度を保つためには肉厚を厚くする必要がある。
高いプレス圧により、成形が難しい高強度のチタン材を成型。金属組織を鍛えて、初速性能と分厚い打感を生む。
通常使用される板材ではなく、丸棒鍛造製法を用いるのは、チタンの金属組織をより緻密で均一なものとし、打感の良さをもたらす鍛流線を発生させるため。高い強度と耐久性を得ることが出来るが、温度管理や加圧の方法など、製造には高度な技術が要求される。
チタン板材を圧延製法で製造。組織の緻密や強度は、丸棒鍛造製法に及ばず、鍛流線も生まれない。
前工程でカップフェースに成型された、周囲の余分な部分を取り除く。
製造精度が高いため、取り代は少ない。
500tの荷重で最終プレス。複雑な偏肉形状を高精度な鍛造によって、設計通り制作できるため、肉厚や重量などの誤差は極小になり、研磨作業の必要は極力少なくする。
複雑な偏肉形状を高精度な鍛造によって、設計通り制作できるため、肉厚や重量などの誤差は極小になる。打球面、フェース裏の研磨はほぼ必要なく、鍛造された時点で、設計どおりの高いCT値(反発性能)を維持できる。
組織が詰まっているため、強度を保ちつつ、反発性能の高さと打感の良さを生む。
フェース部を溶接した溶接痕を手作業で研磨する。予め大きく作って、削って作るのが一般的な製法。人の手による削りが入るため、CT値のばらつきは大きくなる。
フェース内で溶接する一般的な方法と異なり、カップフェースを外周ボディ部で溶接。最終研磨工程で、フェース部分を削る必要がなく、研磨による製品のバラつきを抑えることが出来る。また、溶接の高熱による特性変化の影響もない。
板材のフェースをボディに溶接する一般的な製造方法。
フェース面部分を均すため、手作業による研磨を行う必要がある。この研磨作業によって、反発などの性能に個体差が出やすくなる。また溶接の熱による性質変化の影響もある。
緻密な鍛流線を持ち、ルール限界の高反発エリアを芸術的な高精度で実現する。
ロフト・ライ角、FA、CT値を全製品検査。
特にCT値は、フェースの11箇所を検査し、すべての製品がギリギリの値で完成品となる。
どうしても製造上の個体差が大きくなってしまうため、いわゆる“当たり外れ”も出やすい。